15.2.2023
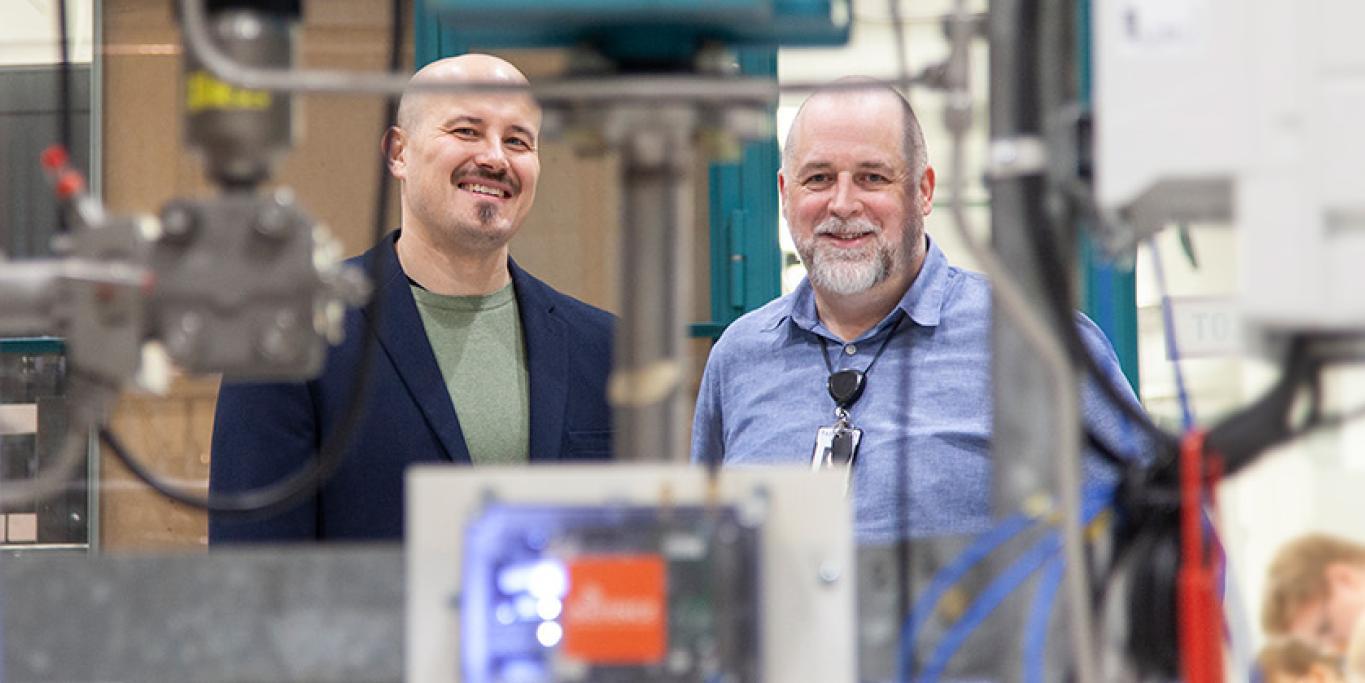
Taitotalo is Finland’s leading vocational adult education centre, serving the educational and training needs of some 18 000 adults every year. It came to be when Amiedu (since 1976) and AEL (since 1922) merged in 2020.
Industrial condition monitoring is going through a fast digitalization phase. Systems such as the Condence solution from Distence are getting a stronger foot hold in leading industrial maintenance organizations, driving the need for training of experts with knowledge of cutting-edge technologies and the understanding of how to best put them to use in their respective organizations. Taitotalo is doing exactly this.
It is no longer enough to have one expert in predictive maintenance in the factory who understands the digital possibilities. The entire staff must be on board with the issue at some level, says Ari Määttä, the maintenance trainer at Taitotalo.
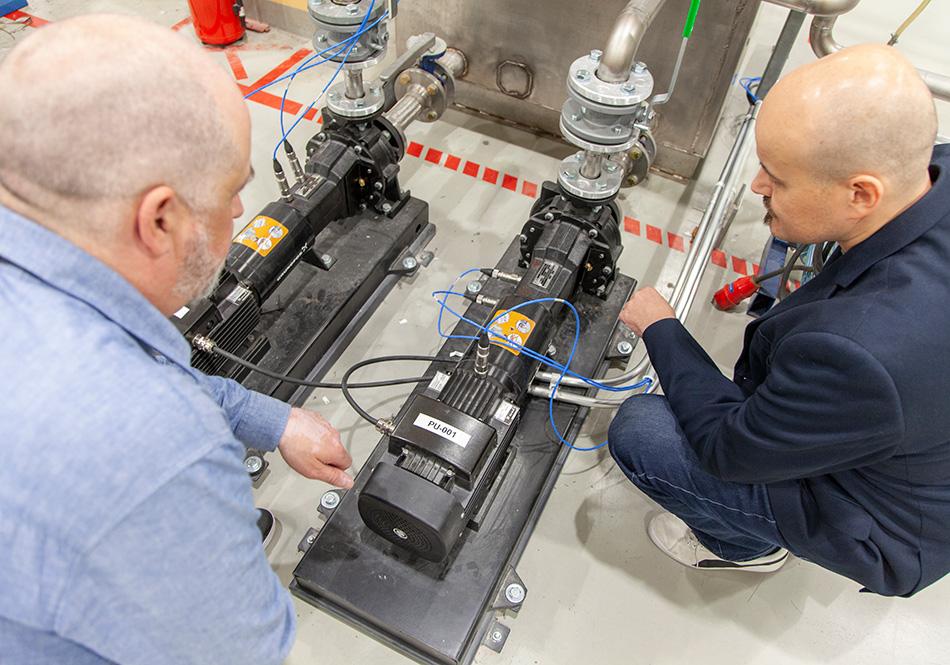
Trainings propagate discussions among participants with diverse backgrounds from different industries. This leads to new thinking and revelations that benefit everyone. The participants go home with new tools and a new mindset.
Digitalization is key if you want to stay at the forefront of reliability as well as to run an efficient and modern service organization. The system detects details in the measurement results that a human being cannot. It can analyze data faster and detect long-term changes. It is good for counting and strong when there are a lot of numbers and data to process. The system makes it easier to detect weak signals, explains Panu Kinnari, COO at Distence.
To give an example, with Condence in pump training we can show how changing alignment or pumping malfunctions affect the whole. By driving the system for longer periods of time in failure mode, we can also demonstrate the predictability of a failure, says Ari Määttä.
New digital systems do not replace people. They help with issues where their time is not at best use and where data processing and analysis can be automated. When inputs come from the system, you have to react to them. For example, if the system tells you that the bearings in the same device are going bad for the third time, it is not enough to change the bearings again. The root cause also needs to be found and fixed, says Panu Kinnari. With systems such as Condence, we can automate monitoring, detect anomalies and trends, and do the data analysis. The professionals can use their time best solving problems that they have expertise for, including problems where creativity and conceptual issues such as risk analysis are involved, not to mention the mechanical work.
Working together with education and training partners benefits the entire maintenance sector.
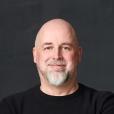